Corrugated boxes use widely types for transportation packaging nowadays. But corrugated boxes are not the same as the cardboard boxes we usually talk about. What exactly is different, and why do you want to use corrugated boxes? Friend, then please read on to learn more about corrugated boxes.
The difference between Corrugated Box and cardboard
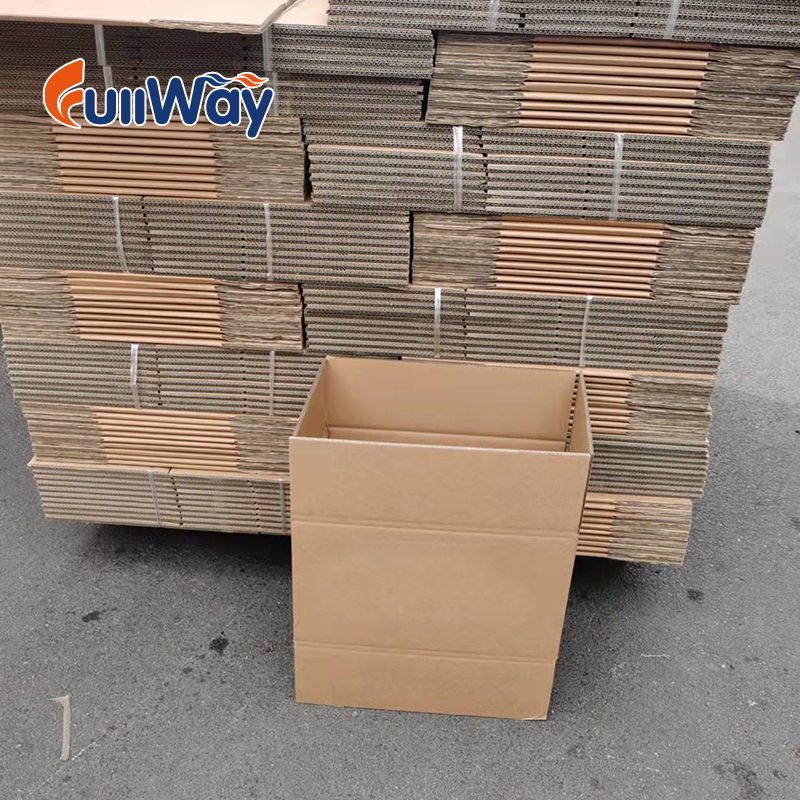
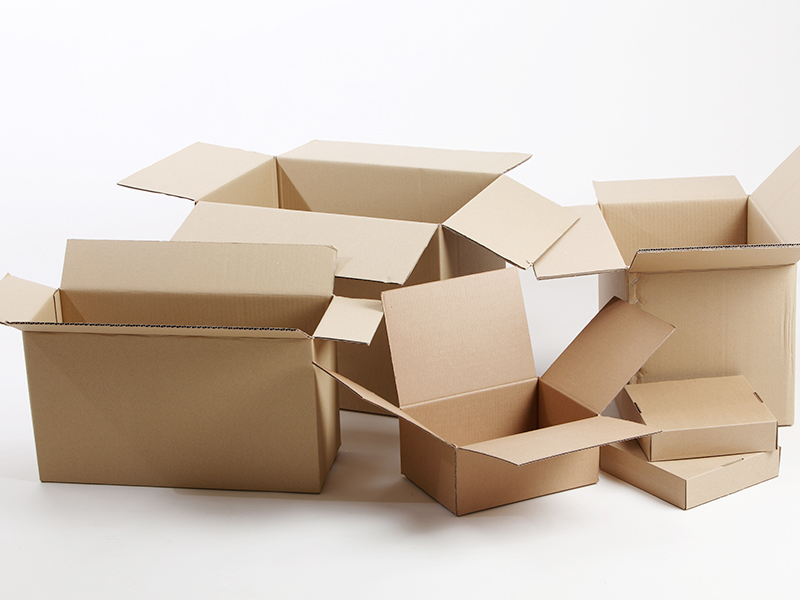
Cardboard boxes do make of thick paper or heavy paper pulp with a smooth surface. Corrugated cardboard boxes do make by laminating multiple layers of cardboard and small internal grooves. This material does use in the manufacture of various product packaging, storage containers, etc. Corrugated shipping boxes are very popular among manufacturers in the transportation of products. It is used to protect goods from occasional collisions or wet conditions. It is also sometimes used to fold clothes to prevent excessive wrinkles.
Corrugated Box Manufacturing Process
Corrugated packaging is one of the most recycled packaging materials on the planet. This is because it is made primarily from trees and sustainably recycled waste shipping corrugated boxes. So it is a renewable resource. Over the past eight years, the industry recycling rate has been about 90 percent. The recycling rate is predicted to reach 96% in 2023. To understand shipping corrugated boxes, we must first know how it is made.
When corrugated box is recycled, the discarded corrugated boxes are sorted, baled, and shredded. Sun-dried pulp is placed on a giant reel. After that, the vast bales are sent to a paper mill. After completing a series of procedures, the corrugated shipping boxes are crushed there. Pulping then takes place in a pulping machine.
The corrugated Box is then cut into individual reels and rewound. This is the complete recycling procedure. These scrolls are fed into a corrugator or a feeder. There, they’re turned into corrugated paper, which is then turned into environmentally-friendly corrugated packaging.
Types of Corrugated Box
You now understand the difference between a corrugated box and a cardboard box. Then we may delve deeper into the fundamentals of corrugated boxes. Regarding corrugated shipping boxes, there are many variables to consider. It’s because of this that they’re so adaptable.
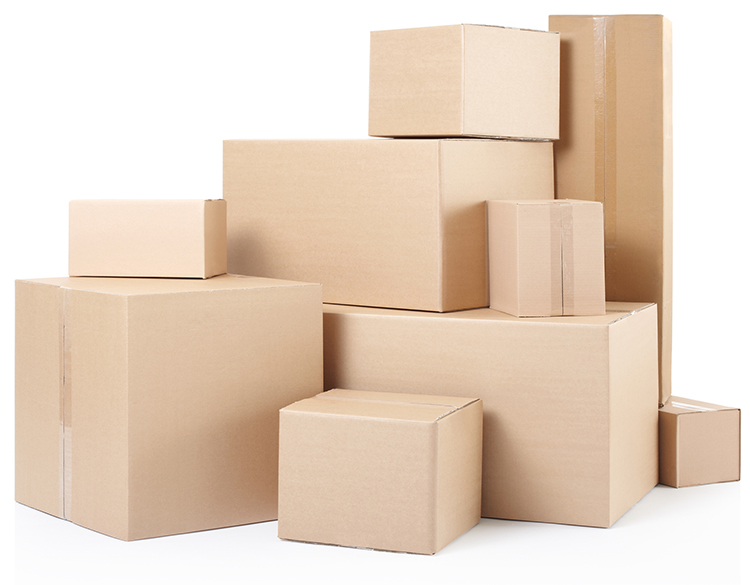
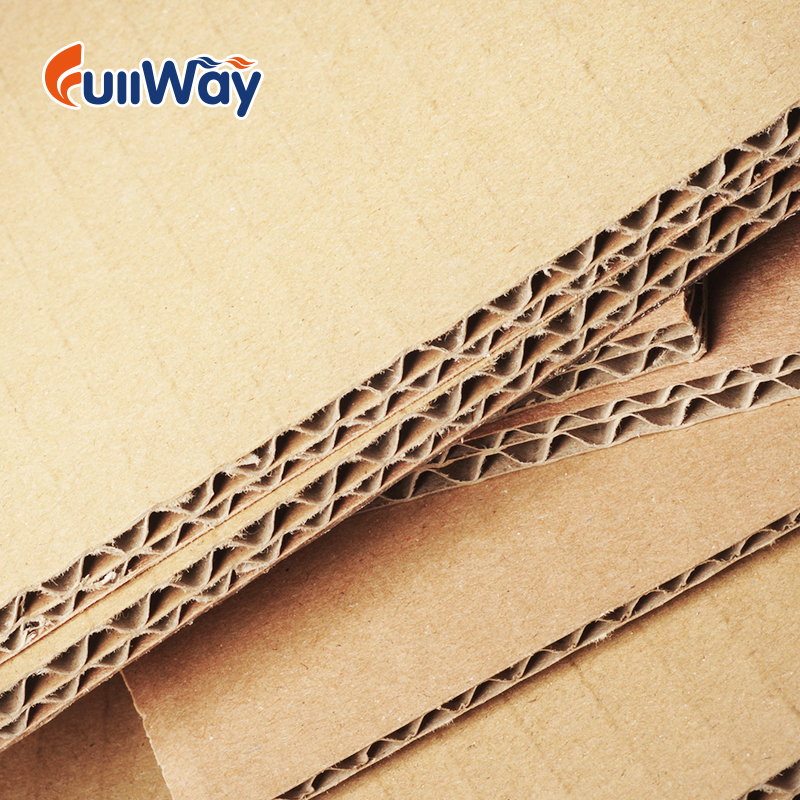
Flute Profiles
A, B, C, E, and F are the most common flute profiles for corrugated shipping boxes nowadays, with A having the largest flute size. The groove size determines the wall thickness and stacking strength of corrugated boxes. The “A” groove is around 5 mm thick and is perfect for products that need extra cushioning or stacking strength. The thickness of the boards does reduce when they pass through the B, C, E, and F grooves, resulting in thinner panels.
Board Types
Corrugate boxes come in four different types of boards. Single-wall and double-wall boards are the most frequent. A single-sided board, made out of a sheet of linerboard attached to a corrugated paper, is also available. We paste corrugated paper between two liner sheets to form a single wallpaper sheet. This allows the product to protect and cushion. The most prevalent type of board on the market is single-wall board, which use for everything from shipping boxes to retail displays.
Two sheets of corrugated paper can place between three sheets of linerboard, which creates a double-wall structure. This type of carton does use when transporting heavier products. Finally, triple-wall refers to three corrugated board sheets between four liner sheets. This is the most durable of all board types and uses for industrial parts or production boxes.
Board grade
Mullen or Edge Crush Test corrugated boxes are two types of corrugated boxes (ECT). The ECT test refers to the stacking pressure or strength it can withstand when crushing a corrugated cardboard box. If you’re stacking corrugated cardboard boxes together on pallets or warehouse shelves, ECT boards are a fantastic alternative.
The Mullen value is the pressure the box can withstand before it bursts or punctures. You want this type of board if you need resistance to internal or external forces.
Benefits of Corrugated Packaging
Efficient
Improve the product’s protection during transit. Use custom corrugated boxes to better pack and ship your goods. Its multi-layer design creates a sturdy cushion for your products’ safety throughout shipping and handling. Corrugated boxes also act as a robust barrier between your products and any outside moisture, ensuring they stay dry while on the road.
Customization
Custom corrugated boxes are available in a choice of thicknesses and sizes as well as coatings, adhesives, graphics and shapes. May custom Almost every feature of corrugated board to meet a company’s products and brand.
Increase Customer Satisfaction
Because e-commerce companies lack the “shelf presence” that shops do, creating a good unboxing experience is vital, they also need to leave a lasting impact on their clients. Make unboxing a pleasurable experience for them.
Eco-friendly
A corrugated board is one of the most cost-effective solutions due to its lightweight and versatile form. There is no need for high-cost labor, tools, or excessive bulk. Corrugated box is also recyclable and reusable. As a result, it’s not only cost-effective, but it also has the potential to improve sales.
Ready to switch your packaging to corrugated?
We hope you now have a better understanding of custom corrugated boxes. Fullway has been using corrugated packaging and mesh bags for years to help businesses connect with their customers. We are the largest corrugated box manufacturer in China. We hope to be your corrugated box manufacturer’s partner..