People often use onion mesh bags in daily life, such as potato mesh bags, firewood mesh bags, and onion bags. Plastic mesh bags are very versatile, but have you ever thought about the manufacturing process of plastic mesh bags when you use onion sacks? What is the printing of onion mesh bags? The following article introduces you, and I hope you all Cherish the environment. Try to choose biodegradable mesh bags for use.
As we all know, the primary material of onion mesh bags is plastic film. So what is the forming process of the plastic film? How to process the molded plastic film to create a onion mesh bag? Do you know these problems?
This is the first step in making onion sacks:
Blow molding and wire drawing.
Blow molding is to blow the purchased raw material plastic particles into a plastic film through a blow molding machine. After the equipment mixes the raw materials and auxiliary materials, they will melt and extrude into a film through an extruder. After that, the raw material enters the extruder, where it is heated externally at a temperature of 190-250°C.
The heated raw materials are extruded out of the machine under mutual shear between the screw and the barrel. Next, put the molten film into the cooling water. After cooling, the machine uses a blade to cut the film into filaments. The embryo silk is stretched at high magnification in a high-temperature oven until a flat yarn appears.
The plastic film is divided into filaments (blanks) by a machine and then stretched and oriented to produce flat filaments. The flat cord is heat-set on the hot roll, shrinks at a low traction speed, and does the process by the cold roll at low temperatures. Finally, these flat filaments are wound on the bobbin to make a spindle.
Weaving
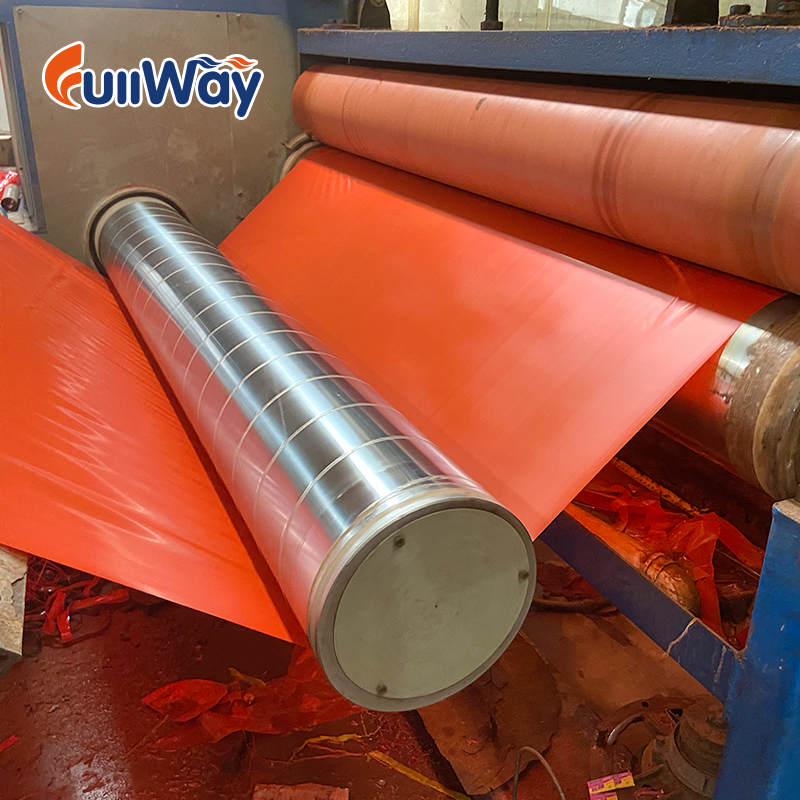
The weaving machine interweaves the warp and weft of the flat yarn to make a cloth. The technology of producing woven fabrics from the flat threads of the mesh bags is to interweave the warp and weft of the matte yarns into materials. The tube cloth is woven with a circular loom, and there are many spindles on the warp frame of the circular loom.
According to the woven fabric and flat yarn width, add the corresponding regular number of warp threads. Before the warp yarn enters the circular loom, the warp yarn will insert into the opening by the brown frame of the warp yarn, and the weft yarn shuttle moves circularly through the warp yarn in the insertion opening to weave into a cheesecloth. A circular loom has several shuttles, and several wefts do weave together. Suppose the warp yarn is changed to split yarn during the weaving process. The finished onion mesh bag can hold heavier items.
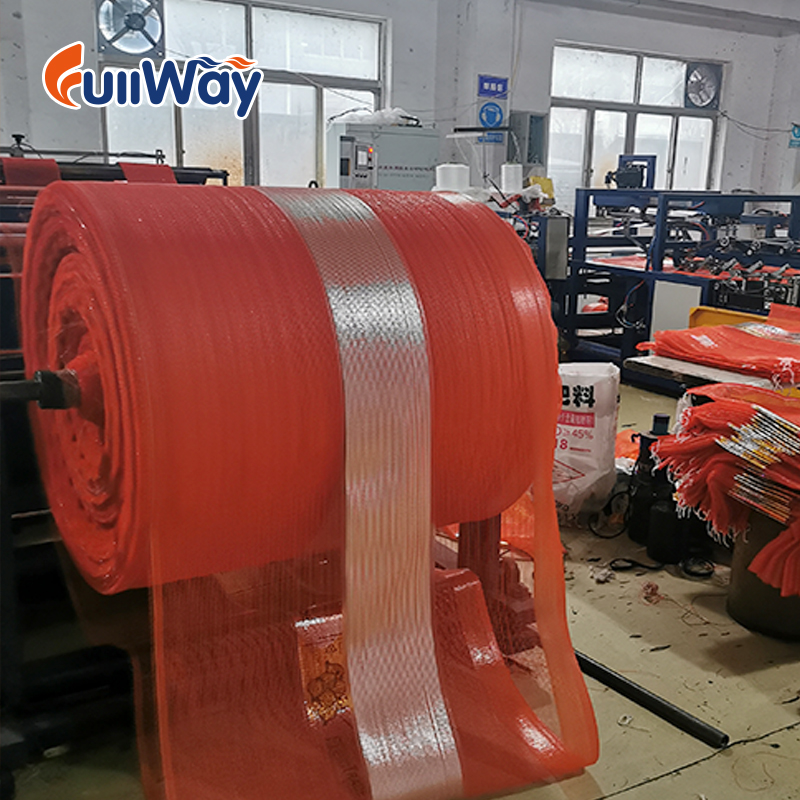
Laminating:
Lay the albuginea and the trademark film in the middle on the correct position of the mesh. (Net bags without trademarks and white film do not need this process) Merchants who need to print logos can negotiate with the manufacturer to print their favorite brands in this step. Businesses printing their trademarks can help increase their visibility.
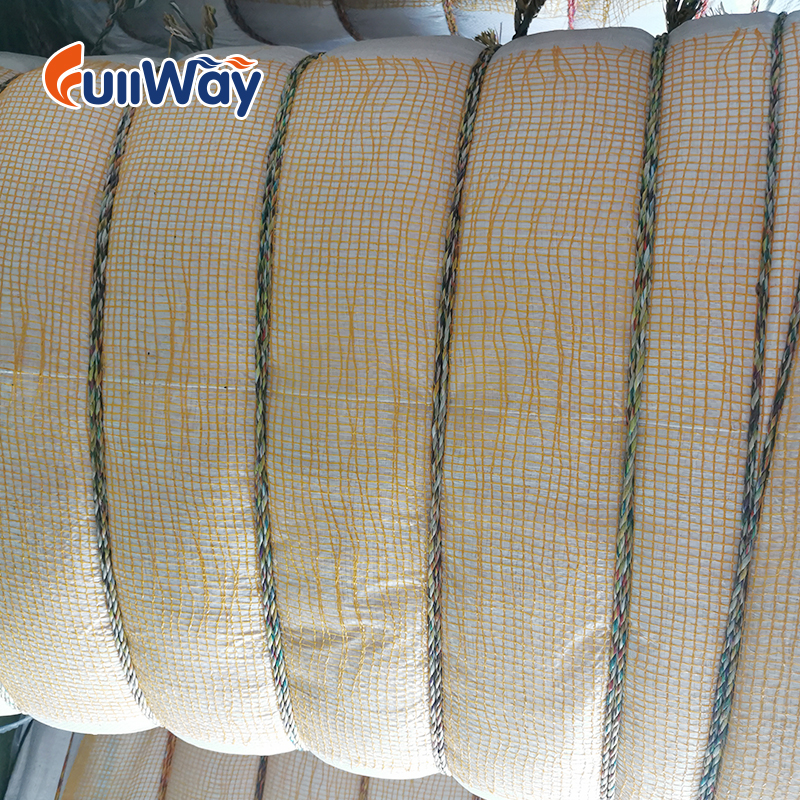
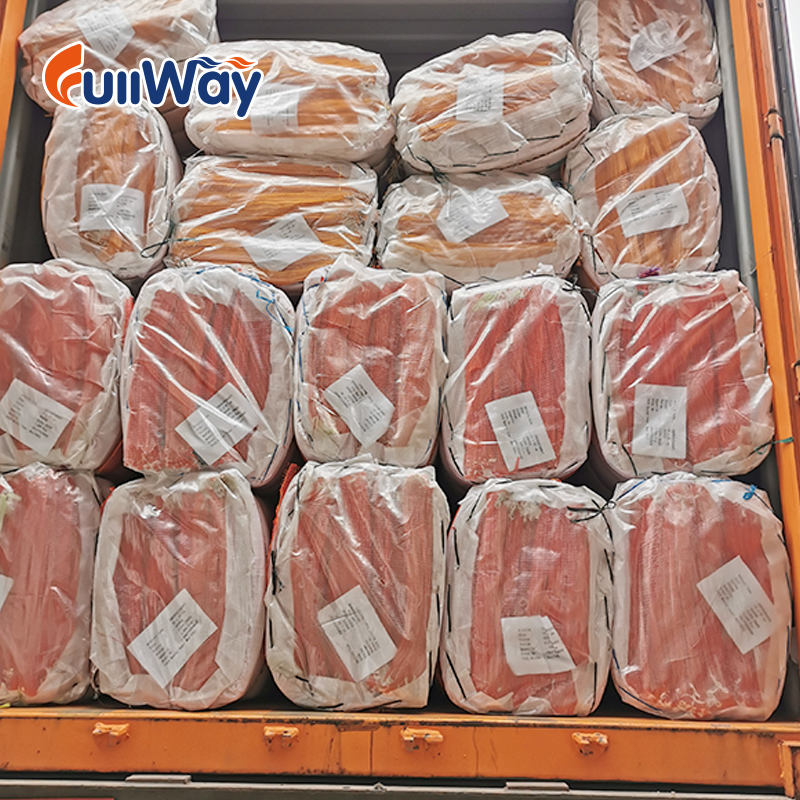
Sewing onion Mesh Bags
Stitching strength index is one of the most critical steps in bag making. This process is very vital. In the national standards for plastic woven bags, GB/T8946 and composite plastic woven bags GB/T8947, the tensile load in the seam edge direction and the seam bottom direction is specified. The main factors affecting the strength of sutures are the types and models of sutures.
For laminating cold-cut bags, crimping is generally used because it may tear out the stitches on the cold-cut edges from the warp threads along with the weft threads. The technical indicators of ordinary woven bag making are mainly the appearance tolerance size, the pull-off force in the seam bottom or seam direction, the clarity of the printing ink and the cleanliness of other parts after printing, the accuracy of the layout position, the stitching stitches, and the stitches: the gap, and the lack of stitches, thread breakage and other requirements.
We usually use the flat stitch method to sew the bottom of the mesh bag and fold the sides three times. The side width of the onion mesh bag should be greater than 32.5px, the flat stitch should be parallel, and the distance between the inner and outer edges of the folded edge should be 1/4. The needle and thread should be inside the fold of the onion net bags, the needle thread density should be low, and there should be no floating threads. When machine processing weaved bags, should knitting the sides and bottom of the woven bags together. Finally, cut the edge of the onion mesh bag with a knife. At this time, the bottom of the mesh bag is double-threaded.
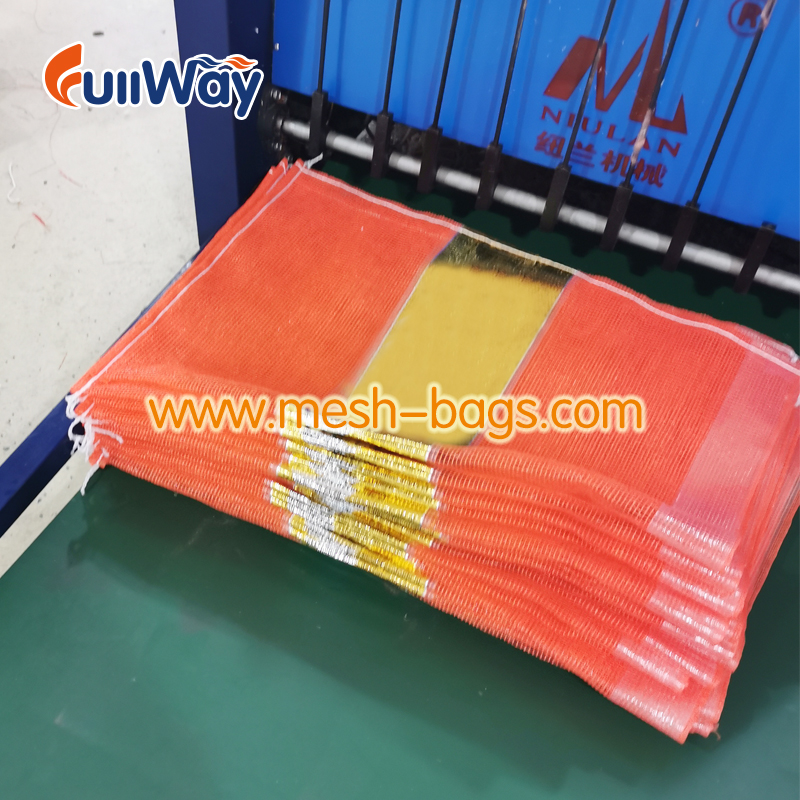
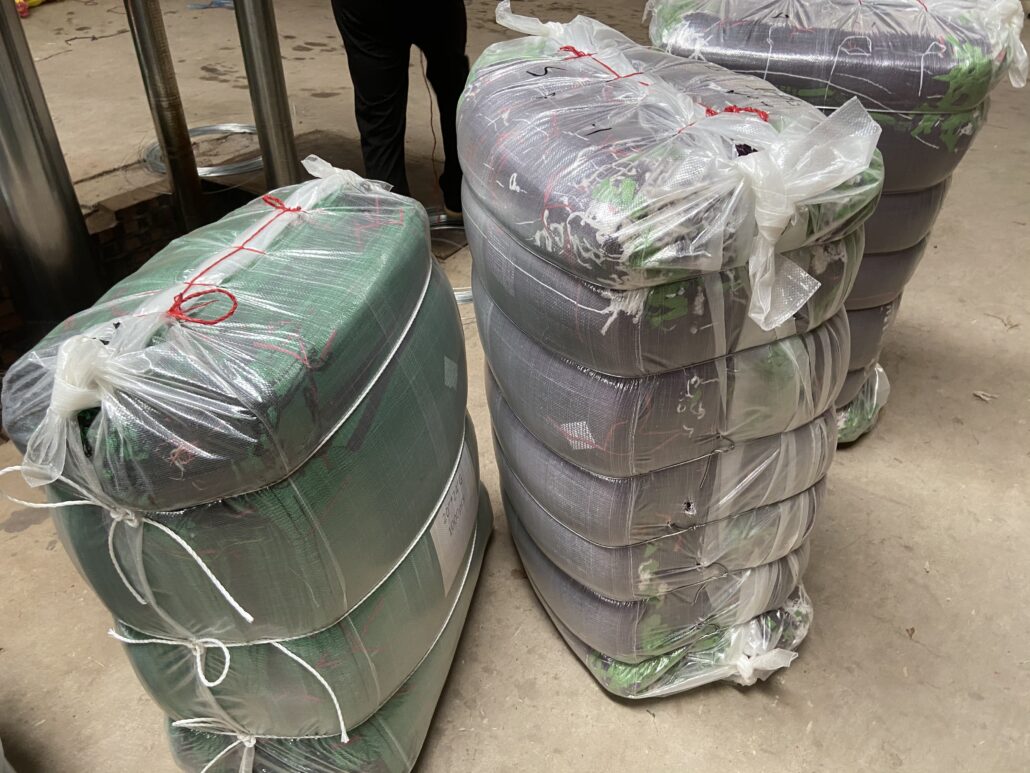
Detection:
After the production is completed, any onion mesh bag must undergo quality inspection. The first is the detection of the length and width of the onion sacks. The size of the two cannot deviate. The second is the color detection of onion mesh bags. The mesh bags wholesale produced in the same batch cannot have noticeable color differences. The third is stain detection.
Newly planted onion mesh bags must ensure that their surface is clean and there are no apparent contaminants on the mesh bags. Should also inspect the edges of the onion net bags. The advantages of the qualified onion mesh bags are neat and without alleged irregularities. The warp and weft threads of the mesh bag are also critical. Each mesh bag promises to have two non-adjacent cables, which must connect firmly.
Punch:
Onion mesh bags that require film covering on their mouths require perforation for filling. For example, onion sacks with a mouth string do not need this process.
Bale:
Bundle the mass-produced onion net bags with a baler. In this way, it is not easy to disperse during transportation and is convenient for handling.
The above is the production process of the net bag. This can also help you to choose the one that suits you when buying onion net bags in the future.